|
Эд Родригес (Перевод Ю. Потапова)
Методы охлаждения DC-DC конверторов
В то время как централизованные автономные сетевые
блоки питания (AC-DC конвертеры), как правило, имеют собственную интегрированную
систему охлаждения, монтируемые в платы DC-DC конвертеры требуют разработки
внешней системы отвода тепла. Правильный способ охлаждения конвертора
может повысить не только его работоспособность, но и надёжность системы
в целом. В настоящее время правильное понимание инженерами происходящих
в системе тепловых процессов так же важно, как и разработка схемотехнического
и конструктивного решения.
Исторически сложилось, что с DC-DC конверторами мощностью
ниже 25 Вт обращаются как с большинством монтируемых на плате компонентов,
при этом они характеризуются максимальным значением рассеиваемой мощности
для некоторой температуры окружающей среды. Конвертеры, рассчитанные на
мощность от 25 до сотен Вт, классифицируются как мощные и характеризуются
максимально допустимой температурой основания, независимо от температуры
окружающей среды, аналогично мощным полупроводниковым приборам.
С точки зрения тепловых процессов, мощный DC-конвертор
может обеспечить весьма большую мощность в нагрузке, но лишь при условии,
что имеется эффективный отвод тепла, который, осуществляемый, как правило,
через многослойную структуру к наружной поверхности корпуса, охлаждаемой
воздухом.
В любом реальном модуле питания имеются специфические
компоненты, являющиеся основными источниками тепла. Защитный металлический
кожух или основание служат для эффективного отвода тепла и уменьшение
разности температур между точками подложки. Для мощных конверторов, имеющих
металлическое основание или радиатор, теплопроводность основания приобретает
гораздо большее значение, чем просто передача тепла окружающему воздуху.
Основание выполняет две функции: равномерного распределения
температуры от локальных источников тепла, которыми являются полупроводниковые
приборы, и передачи тепла в радиатор.
Отметим, что основное внимание следует уделять отводу
тепла именно от полупроводниковых приборов, так как они производят в среднем
около 85% генерируемого тепла и больше всего критичны к системе его отвода.
Как правило, увеличение температуры перехода на каждые
10° приводит к снижению надёжности полупроводниковых устройств на 50%.
Именно поэтому проблема охлаждения блока питания или конвертора выходит
за рамки простых оценок и становится важным фактором повышения надёжности
этих устройств, выраженной в среднем времени наработки на отказ.
Основным фактором обеспечения максимальной производительности
конвертора является эффективность передачи тепла от поверхности к воздуху,
характеризуемая тепловым сопротивлением. Чем ниже тепловое сопротивление,
тем лучше отвод тепла. На практике, распределение тепла внутри устройства
никогда не является равномерным, всегда имеются так называемые “горячие”
точки. Например, если источником тепла является кристалл МОП-транзистора
или выпрямительная диодная сборка, то передача тепла от него осуществляется
по конусообразному каналу (конической тепловой трубе) аналогично тому,
как распространяются звуковые волны или свет. Но из-за того, что источники
тепла имеют определённые размеры и конфигурацию, точного конуса не получается.
Изображённая на рис. 1 цепочка тепловых сопротивлений отображает типичный
путь отвода тепла от мощного полупроводникового прибора DC-конвертора.
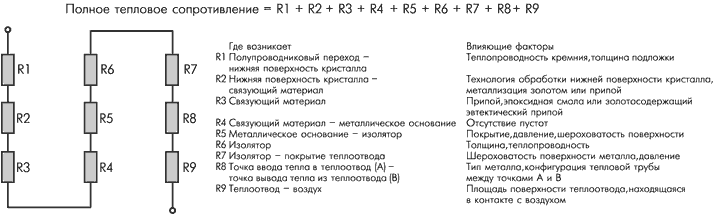
Передача тепла из одного места (например, кристалла)
в другое (окружающий воздух) определяется толщиной слоёв и тепловым сопротивлением
материалов, а также площадью их касания (чем больше площадь касания, тем
большее количество тепла может быть передано).
Часто недостаточное внимание уделяется тому факту, что
неблагоприятный эффект от воздействия высокого теплового сопротивления
увеличивается по мере приближения к источнику тепла. Иначе это можно проиллюстрировать
так: чем дальше от источника тепла находится слой материала, тем шире
в этом месте конус тепловой трубы, а значит снижается влияние теплового
сопротивления этого материала. Всё это означает, что даже самый хороший
теплоотвод с вентиляцией не обеспечит охлаждения кристалла микросхемы,
если переходы кристалл–корпус и корпус–теплоотвод имеют неоправданно высокие
значения теплового сопротивления.
На практике это означает, что в некоторых приложениях
простое увеличение площади подложки может обеспечить более эффективный
отвод тепла, чем использование сложного радиатора с вентилятором.
Алмаз
Серебро
Чистая медь (без кислорода)
Холоднотянутая медная проволока
Бериллиево-медный сплав
Алюминий
Оксид бериллия BeO
Латунь
Кремний
Окись алюминия
Припой из олова и свинца
Нержавеющая сталь
Эпоксидные смолю, полиуретаны и силиконы
с наполнителем из окиси алюминия
Дистиллированная вода, стекло
Пластмассы, эпоксидные смолы, стеклотекстолиты,
теплопроводящие пасты, силиконы, слюда
Воздух
|
25000
20000
17000
13000
7000
8000
7000*
5000
3000
1200*
1100
900
50–250*
40*
10–30*
1*
|
*) диэлектрики.
В таблице приведена относительная теплопроводность различных
материалов, наиболее часто применяемых в электронной промышленности. Для
большинства инженеров может быть интересным тот факт, что все эпоксидные
смолы, пластмассы, кремнийорганические соединения (даже арахисовое масло)
падают в узкую полосу значений относительной теплопроводности между 5
и 30, и что нет более теплопроводящего материала среди них, чем эпоксидная
смола, если только в качестве наполнителя не используется оксид алюминия.
Разумеется, различные сорта эпоксидных смол имеют различную теплопроводность,
однако, толщина слоя и площадь касания здесь могут перевешивать относительную
теплопроводность при выборе конкретного материала.
Методы охлаждения
В DC-DC конверторах эффективность отвода тепла может
быть увеличена за счёт использования одного или нескольких снижения теплового
сопротивления, а значит удельной теплопроводности от внутренних источников
тепла в окружающую среду:
- использование большого металлического элемента, обеспечивающего увеличение
диаметра конической тепловой трубы, а значит и эффективность отвода
тепла в окружающий воздух. Этот метод не всегда применим к мощным конверторам,
так как изначально считается, что габаритные размеры конвертора должны
быть малы;
- принудительный обдув воздухом подложки или корпуса конвертора, который
ускоряет процесс отвода тепла за счёт увеличения диаметра конической
тепловой трубы. Этот метод хорошо изучен и не представляет собой ничего
удивительного. Степень охлаждения здесь имеет ярко выраженную зависимость
от скорости воздушного потока и площади обдуваемой поверхности, поэтому
может быть оценена без особого труда. Обычный вентилятор развивает скорость
потока воздуха около 100 м в минуту и этого вполне хватает для эффективного
охлаждения типового DC-DC конвертора. Увеличения скорости потока воздуха
до 250 м в минуту достичь, как правило, трудно, а получаемый при этом
эффект непропорционален затратам;
- крепление корпуса к большому металлическому элементу шасси, в результате
чего достигается суммарное увеличение поверхности теплоотвода. Как правило,
использование этого метода затруднено при больших размерах конвертора;
- крепление металлического основания к ребристому обдуваемому теплоотводу.
Использование ребристой поверхности равносильно увеличению площади простого
плоского радиатора (аналогично пункту 3), но позволяет получить более
компактные конструкции. Важно понимать, что эффективность ребристых
радиаторов снижается, если направление воздушного потока совпадает с
направлением рёбер. Как правило, это самый распространённый способ охлаждения
электронных устройств. На практике, использование ребристого радиатора
высотой 1–2 см позволяет удвоить теплоотдачу конвертора по сравнению
с обычным плоским основанием.
На эффективность отвода тепла влияют высота рёбер, зазор
между ними, скорость воздушного потока и его направление. Общая ошибка
разработчиков состоит в том, что при выборе системы охлаждения они оценивают
объём прокачиваемого воздуха за единицу времени. Число кубометров в минуту
ничего не говорит нам о скорости воздушного потока, который должен пройти
вдоль нагретой металлической поверхности, определяется в метрах в минуту
и является главной характеристикой охлаждающей системы.
Маленький вентилятор, удачно скомпонованный с ребристым
радиатором, может оказаться гораздо эффективнее большого вентилятора,
обдувающего плохо продуманный теплоотвод, аналогично тому, как маленький
вентилятор, направленный в лицо с расстояния десяти сантиметров, обдувает
лучше чем огромный вентилятор, расположенный на расстоянии нескольких
десятков метров.
Теоретически имеется бесконечное число возможных схем
охлаждения, на практике используется ограниченный набор конструкций ребристых
радиаторов, обеспечивающий приемлемое решение практически для любой системы.
При построении системы охлаждения конвертора следует
учитывать, что во время эксплуатации могут возникнуть, например, изменения
в температуре окружающей среды или ухудшения доступа воздуха, что приведёт
к снижению эффективности отвода тепла. Тем не менее, использование рекомендуемых
теплоотводов позволит избежать катастрофических отказов оборудования.
Типы теплоотводов
Теплоотводы для наиболее популярных конфигураций DC-DC
конверторов “half brick” и “full brick” производятся несколькими фирмами
и представляют собой ребристые радиаторы для продольного или поперечного
потока воздуха. Для обеспечения максимальной эффективности работы теплоотвода
ребра радиаторов располагают вдоль направления потока охлаждающего воздуха.
Использование теплоотводов
Для эффективной передачи тепла от основания конвертора
к радиатору необходимо использовать специальные теплопроводящие пасты
или прокладки, сглаживающие естественные неровности поверхностей. Чем
больше шероховатость поверхностей, тем толще должен быль вспомогательный
слой. В этом качестве используются:
- теплопроводящая паста (смазка) — прекрасный способ соединения относительно
плоских и даже плохо согласованных поверхностей, однако при этом необходимо
обеспечить очень толстый слой. Неудобства: низкая технологичность, большие
временные затраты и загрязнение;
- тонкая алюминиевая фольга (0,051–0,076 мм) с или без парафинового
покрытия с обеих сторон. Парафиновое покрытие обеспечивает заполнение
микроскопических неровностей на касающихся поверхностях. Неудобства:
фольга должна прокладываться без складок, которые резко ухудшают теплопередачу;
наличие двух поверхностей соприкосновения вместо одной;
- тонкая прокладка из теплопроводящего, но изолирующего материала, например,
каптона или полиамидной пленки. Основное преимущество — возможность
обеспечить электрическую развязку между конвертором и радиатором. Неудобство
— худшая теплопроводность, чем у алюминиевой фольги;
- эластомер на основе силикона. Для конверторов, как правило, используется
слой толщиной 0,127–0,254 мм. Хотя такие прокладки очень технологичны,
они не так хороши, как проводящие пасты и парафинированный алюминий.
Однако, при использовании наполнителя из окиси алюминия эластомер может
быть весьма эффективен, особенно когда площадь касания превышает см2,
а также когда поверхности не являются достаточно плоскими. Неудобство:
тепловое сопротивление эластомера зависит от давления, поэтому при неаккуратной
сборке может произойти непредвиденное снижение теплопроводности, приведодящее
к выходу из строя мощных полупроводниковых приборов при работе в жёстких
условиях и в критическом режиме;
- более толстый слой эластомера на основе силикона (0,508–0,762 мм и
выше), предназначенный для соединения грубо обработанных металлических
деталей, где имеется большая вероятность возникновения зазоров и, как
следствие, снижения теплопроводности. Неудобство — относительно низкая
эффективность передачи тепла, однако лучшая, чем у обычного воздуха;
- материалы, изменяющие свое физическое состояние. Такие материалы представляют
собой специально изготовленные слоистые структуры из парафина или воска,
выпускаемые в виде больших листов или специально нарезанных прокладок
по форме кристаллов. После размещения прокладки между двумя металлическими
поверхностями изделие нагревают до температуры 60–70°C. Парафин тает
и почти идеально заполняет микротрещины. Для плоских металлических деталей
данный метод является лучшим, сравниться с ним может разве что пайка.
Есть несколько советов, которые позволят правильно спроектировать
систему отвода тепла. Прежде всего надо помнить базовую тепловую схему,
изображённую на рис. 2. При надлежащем тепловом сопротивлении даже самый
маленький кристалл мог бы рассеивать тысячи Вт энергии. Ключом к успеху
является знание методов построения систем охлаждения и особенно их стоимостных
характеристик, а также понимание проблем сокращения тепловых сопротивлений.
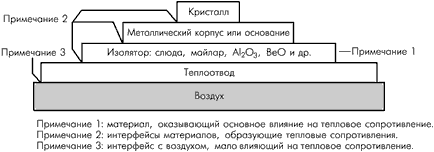
Далее необходимо знать, какие из материалов наиболее
подходят для каждого конкретного приложения. В зависимости от технологии
изготовления теплоотвода его поверхность (гнутая, штампованная, фрезерованная
или полированная) может иметь неровности до 0,254 мм по всей площади и
до 0,508 мм в отдельных местах.
Наличие таких больших зазоров может привести к выходу
модуля из строя вследствие его перегрева. В этом случае оптимальным является
использование эластомера, который хотя и не обладает высокой теплопроводностью,
но при использовании в местах, где диаметр теплового конуса достаточно
велик, может работать намного эффективнее, чем воздух (таблица). В случае
использования эластомера произойдёт некоторое ухудшение характеристик
модуля, но главное, что он сохранит свою работоспособность.
По мере приближения к кристаллу начинают работать другие
правила выбора материала теплопроводящей прокладки. Площадь соприкосновения
здесь не превышает 6,45 мм2, а неровности поверхностей будут минимальны.
Так как в этом случае тепловой интерфейс находится в узкой части тепловой
конической трубы, прокладка должна иметь минимальную толщину и максимально
возможную теплопроводность.
Идеальной здесь была бы пайка. Сразу за ней идёт использование
теплопроводящих паст, но для этого необходимо высокое давление, чтобы
частицы пасты проникали во все микротрещины материалов. Однако для очень
малых областей оптимальным будет использование тонкой изолирующей плёнки
с парафиновым покрытием, а для несколько больших областей — эластомера.
При использовании повышенного давления (каптон, паста,
парафинированный алюминий или чистый парафин) следует убедиться, что процесс
идёт правильно и помогает заполнению микротрещин на поверхностях. При
больших уровнях рассеиваемой мощности зазор даже в 0,025 мм может привести
к резкому ухудшению параметров устройств.
Наконец, следует упомянуть изоляционные материалы, традиционно
применяющиеся в военной и промышленной аппаратуре. Оксид алюминия, оксид
бериллия и нитрид алюминия по своим теплопроводящим свойствам превосходят
все ранее упомянутые пластичные материалы, но требуют принципиально иного
подхода при сборке, что приводит к повышению стоимости оборудования. Ранее
здесь была очень популярна IMS-технология (Insulated Metal Substrate).
В IMS-технологии для достижения требуемой электрической
развязки и хорошей теплопроводности используется слоистый материал из
медной фольги, полиамида и окиси алюминия. Стоимость такой технологии
достаточно высока, зато она даёт превосходные результаты.
В заключение следует сказать, что какой бы из методов
охлаждения не использовался, необходимо обеспечить качественный путь для
отвода тепла с использованием наиболее подходящих для этого материалов.
Разумеется, для реализации проекта важно понимание физики всех проходящих
в системе процессов.
CIE, ноябрь 1999
|